Formation and Aging Intelligent Manufacturing Turnkey Solutions for Prismatic Cell
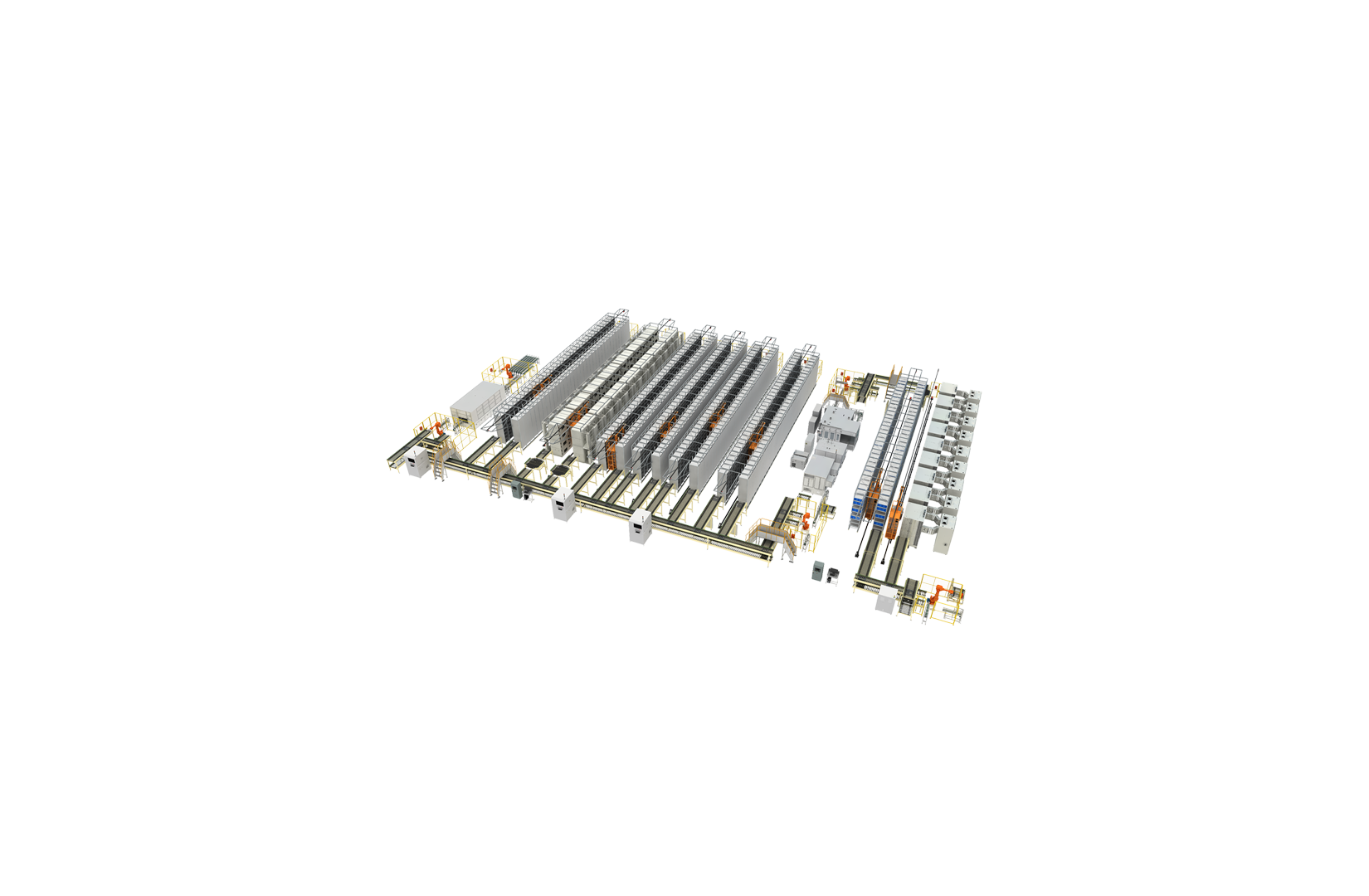
Our prismatic cell formation and aging production line adopts industry-leading integrated technology with PCS and precision water-cooling/water-heating systems, delivering comprehensive solutions for lithium-ion prismatic battery production.
This complete lithium-ion battery manufacturing equipment covers the entire production process:
· High-temperature aging manufacturing for cell stabilization
· Nail extraction/insertion and high-temperature vacuum formation manufacturing
· 2nd electrolyte filling and sealing nail welding
· 2nd helium leakage testing
· Room-temperature aging manufacturing
· OCV testing, capacity grading, film wrapping and final sorting
The line features intelligent logistics throughout the battery production process, enhanced by our self-developed FGS and BIMP, enabling fully automated and smart factories for efficient lithium-ion battery manufacturing.
As specialists in lithium-ion battery manufacturing equipment, we provide turnkey solutions for both LiFePO4 and conventional lithium-ion prismatic batteries production, earning the trust of globally renowned battery manufacturers.